Valve services
Maintenance, repair and modification
Our many years of experience in the field of ball valves with diameters from 25 to 2,600 mm (DN 1" - 104") enable us to apply our expertise in the maintenance and repair of ball valves, even during plant operation.
In addition, we offer the production of spare parts, such as ball and seat rings using special ball and vertical lathes.
Valves severely damaged by corrosion are refurbished by cladding and hardfacing sealing surfaces including respective PWHT measures in such a way that they are equivalent to new fittings.
In addition, safety valves, control valves, slides, flaps and drives can be repaired, refurbished and even modified at the Gladbeck plant for all manufacturers. For modifications and improvements we feature supports made of PEEK (Polyether ether ketone), replacing conventional sealing rings by U shaped rings with preloaded springs or substituting tongue springs by compressed spring types. In some cases, existing ball valves can also be upgraded to "fire safe".
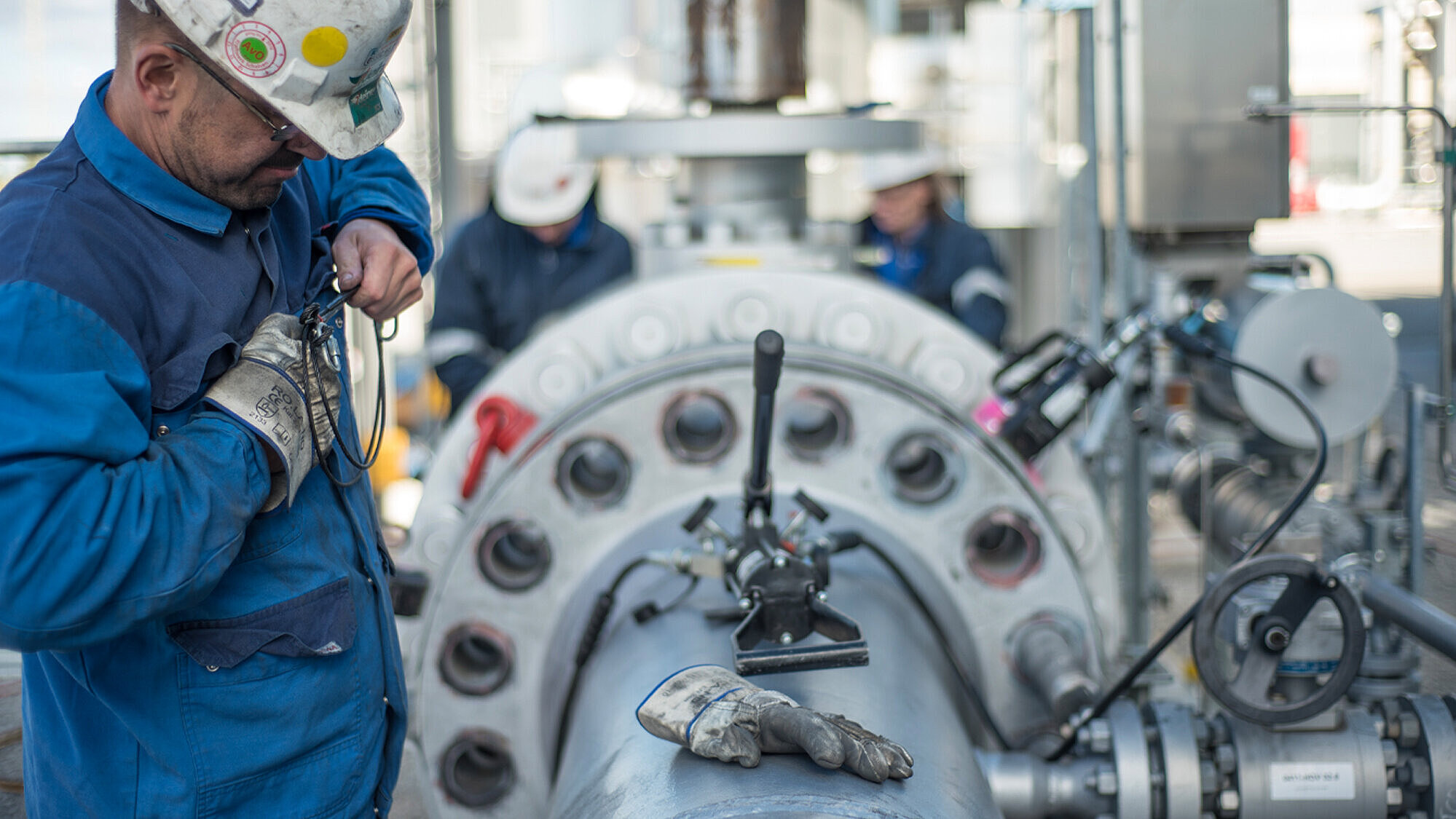
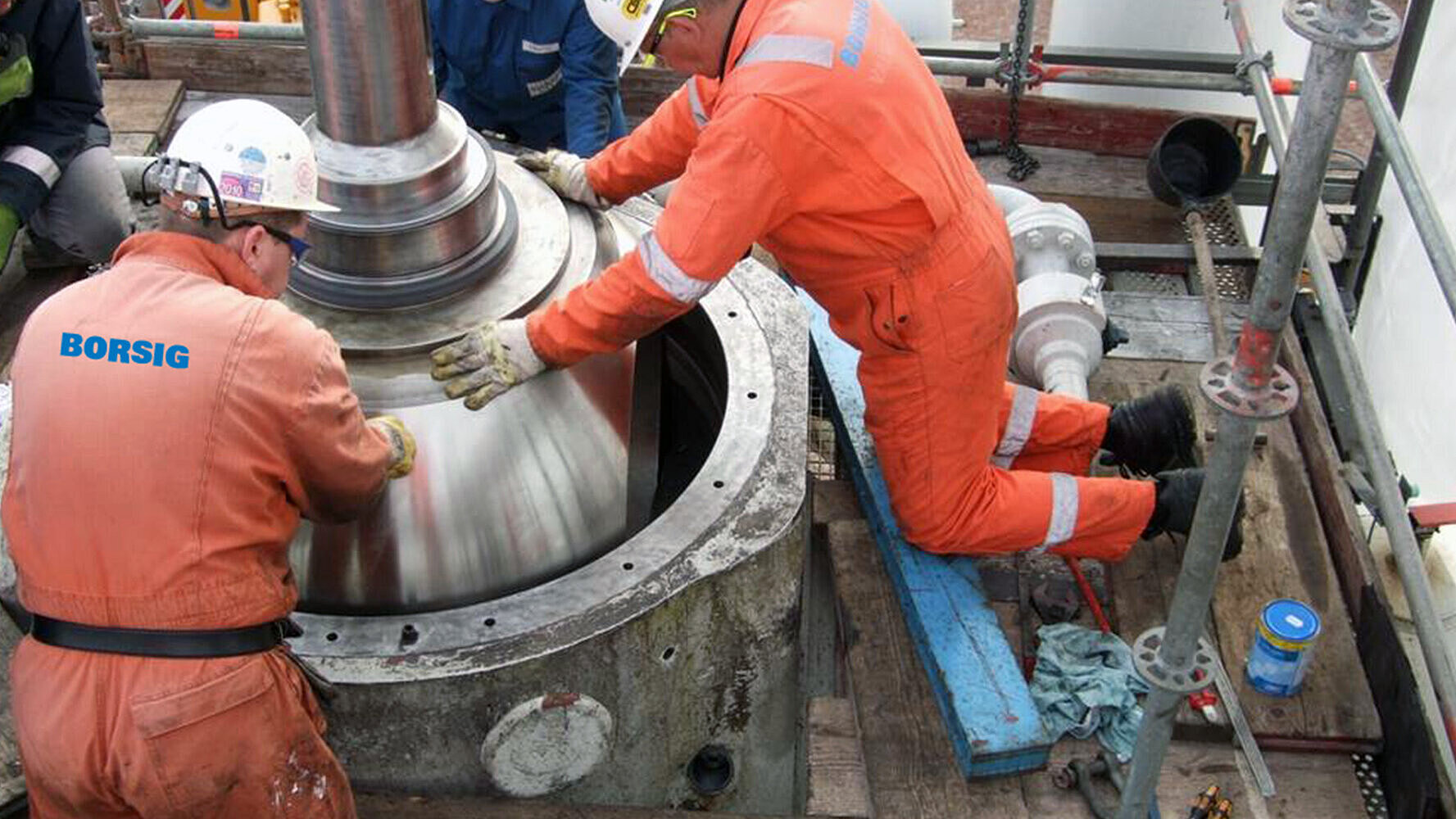
Spare parts
Our internationally active ball valve spare parts service offers sound technical advice as well as individual solutions for BORSIG's own and third-party valves and the corresponding drives and control systems.
Urgently required replacements or other customer-specific orders can be processed and delivered as quickly as possible using internationally available ball valve fittings in our database.
On-site service
Our field service team provides fast and professional on-site service, both scheduled and unscheduled. When operations are interrupted or damage has occurred we offer quick and reliable repair and spare part service. Whether it is a critical or severe service application for power generation, oil & gas or petrochemical industry, our field service technicians can address our clients’ operational challenges.
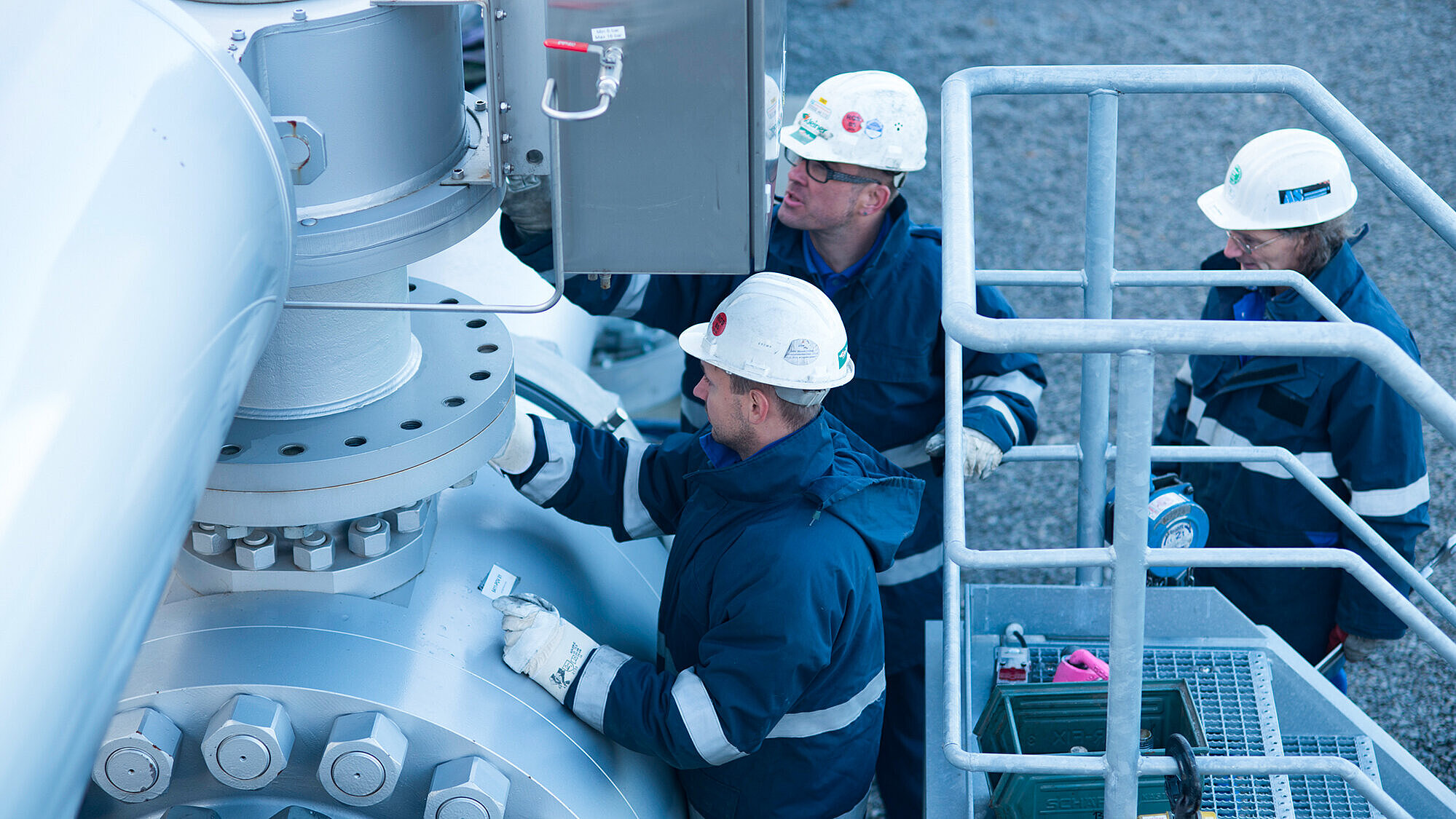
Our scope of service includes but is not limited to:
- Mobile workshop including tooling and blasting container
- Mobile valve grinding and lathe machinery
- Mobile valve testing
- On-site maintenance, disassembly, inspection and repair or replacement of unserviceable components
- Determination of spare part demand
- Installation, commissioning and start-up assistance
- Crane and transport management
- Field support and emergency service
Maintenance, Repair & Testing
We combine the engineering capability from our OEM background with the open-mindedness of an independent service provider. Giving you sound advice and optimal service when it comes to repairing, retrofitting or servicing any type of industrial valves.
After reassembly all valves are subject to a comprehensive performance test according to API6D, PED 97/23/EG and DIN3230 or to customer specific requirements before returning to site.
Our maintenance and repair capabilities include:
- In-house disassembly, inspection and repair or replacement of unserviceable components
- Mechanical machining such as milling, grinding, turning, and lapping
- Life time extension e.G. special coatings for additional protection against wear, erosion and corrosion
- Valve-retrofit e.G conversion from soft seated sealing to metal-to-metal seating
- Valve modernization e.G. application of automation technology
In house test capabilities:
- Hydrostatic shell test
- Seat tests (leackage rate)
- Cavity refief testing
- Double block and bleed testing
- Double isolation and bleed testing
- Torque testing
- Antistatic testing
- Dye penetrant testing
- Positive Material Identification – PMI
- Coating thickness measurements
- Coating thickness
Service Agreements
The intervals between valve maintenance vary according to valve type and operating conditions such as temperature, pressure, media and cycle of operation. For complete peace of mind artec AIS offers flexible service agreements for scheduled maintenance based on:
Long-Term Parts Agreement - LTPA
- Planning support for planned maintenance
- Supply of new or reconditioned parts
- preferential conditions for valve parts or services (covered by the agreement)
- eliminates the risk of unexpected price fluctuations
Long-Term Service Agreement - LTSA
- Planning support and execution of outages on time and material basis
- Supply of new or reconditioned parts
- Provision of supervision and skilled on-site service staff