Pervaporation
Pervaporation is a membrane process which enables solvent dehydration without dependency on vapor/liquid equilibrium. The separation mechanism is based on the high water affinity of the membrane material. Water is easily and preferentially adsorbed and permeated through the dense membrane.
The process can be operated with liquid feed (pervaporation) or with vapor feed (vapor permeation) and in batch or in continuous mode, depending on the feed flow as well as on production needs.
Pervaporation is a state of the art technology for solvent dehydration and methanol separation from organic solvent mixtures especially for azeotreopes.
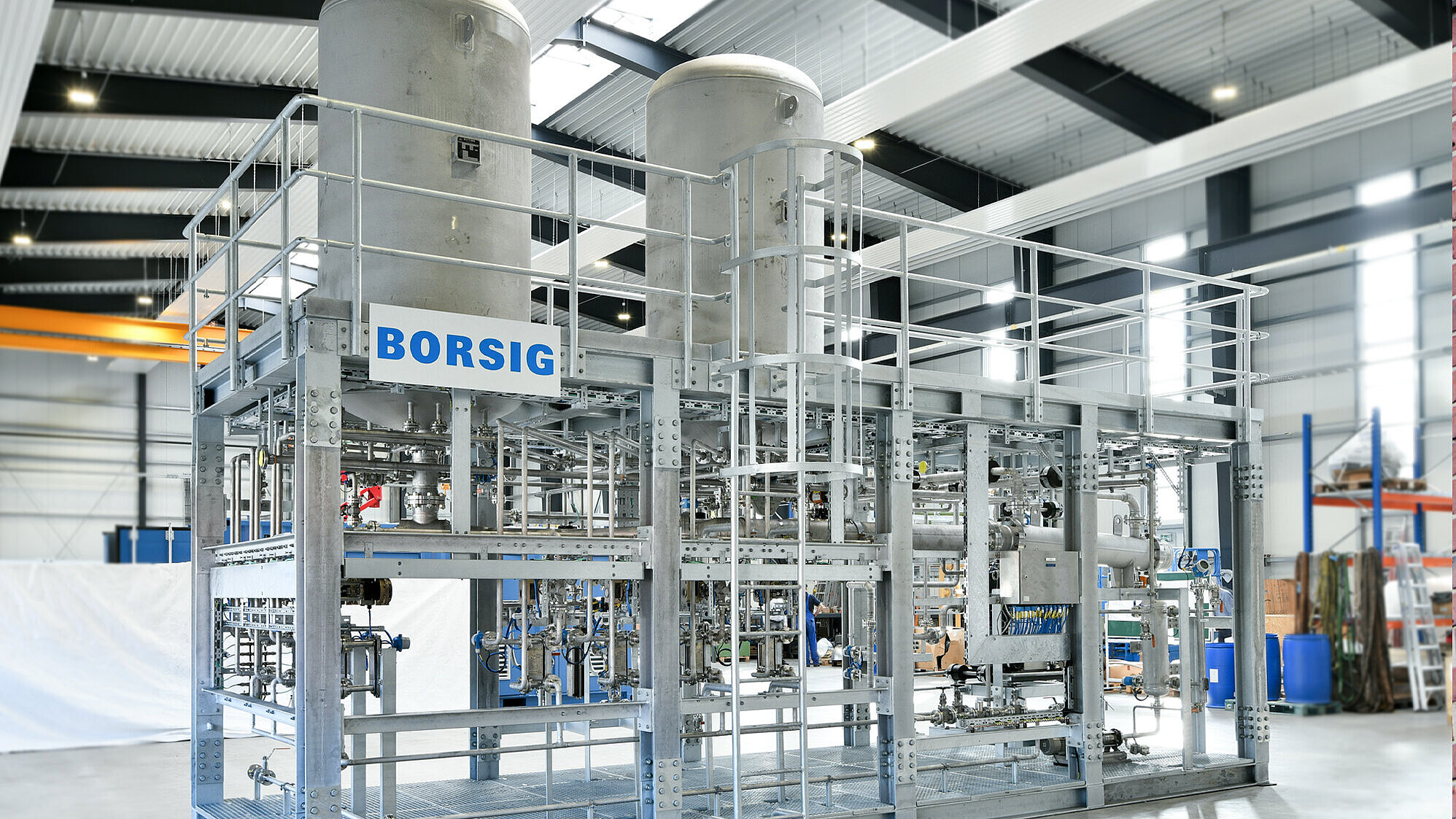
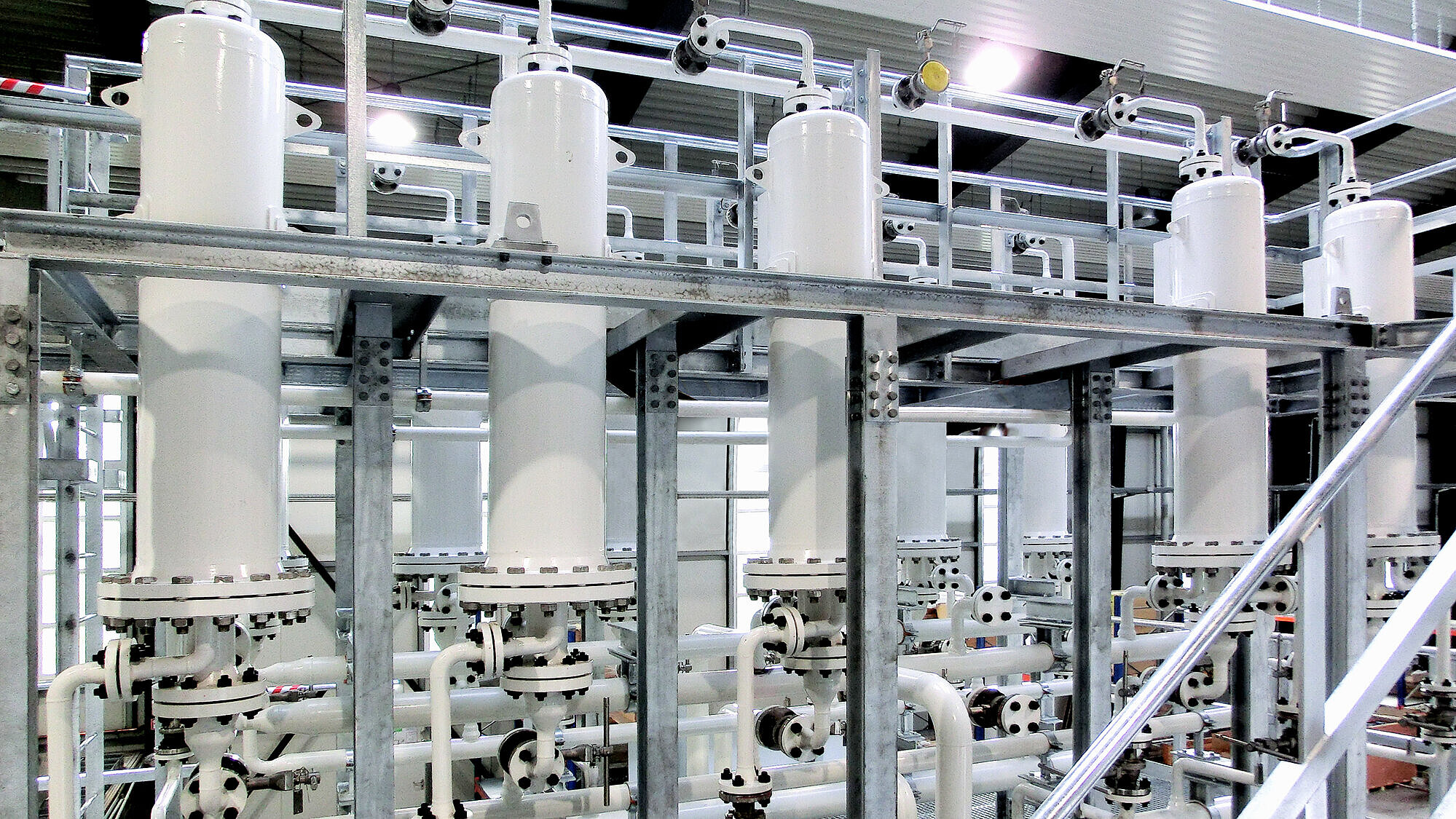
Application
Ethanol is used as solvent in pharmaceutical and nutraceutical processes as well as in the fine chemical industry. The used Ethanol needs to be dehydrated before recycling into the process. By combining distillation and vapor permeation the ethanol can be dehydrated down to water contents of 0.3 wt-% without the use of entrainer or molecular sieves.
For use in biofuel production the water contents in ethanol has to be significantly reduced. Pervaporation plants allow for reduction of water contents down to 0.3 wt-%.
IPA is used as solvent in pharmaceutical and fine chemical production processes, e.g. for the synthesis and purification of pharmaceuticals. The used IPA often contains water and impurities which need to be removed for recycling and reuse.
Liquid feeds consisting of more than 50 wt-% IPA and water can be efficiently dehydrated in pervaporation, vapour permeation or hybrid (distillation combined with vapour permeation) plants.
For synthesis of pharmaceuticals such as Active Pharmaceutical Ingredients (APIs) different solvents are used. Those solvent need to be purified from water for reuse. Multipurpose plants are designed for dehydration of different solvents like ethanol, isopropanol, acetone, tetrahydrofuran (THF), methyl ethyl ketone (MEK) or ethyl acetate by using the same membrane and plant.
In the production of Polyvinyl Alcohol (PVA) a large amount of methyl actetate/methanol mixture is formed in the second production step.
In conventional processing an energy-intensive extractive distillation step is applied to separate methanol from methyl acetate.
By combining distillation with pervaporation the separation process is significantly simplified and no third component needs to be introduced.
In trimethyl borate production process the reaction mixtures is distilled producing a trimethyl borate / methanol azeotrope as the top product of the column. In conventional process, the azeotrope is washed out with a complicated alkali salt process, followed by another distillation step. The addition of a vapour permeation unit in between these two distillation columns is today’s state of the art optimized process with the final product free of salt impurities.
Product/solvent examples
Alcohols
- Ethanol C2H6O
- Propanol * C3H8O
- Butanol * C4H10O
- Pentanol * C5H12O
- Cyclohexanol C6H12O
- Benzyl alcohol C7H8O
- * all isomers
Esters
- Methyl acetate (MeAc) C3H6O2
- Ethyl acetate (EtAc) C4H8O2
- Butyl acetate (BuAc) C6H12O2
Ethers
- Methyl t.-butyl ether (MTBE)C5H12O
- Ethyl t.-butyl ether (ETBE) C6H14O
- Di-isopropyl ether (DIPE) C6H14O
- Tetrahydro furan (THF) C4H8O
- Dioxane C4H8O2
Ketones
- Acetone C3H6O
- Butanone (MEK) C4H8O
- Methyl isobutyl ketone (MIBK) C6H12O
Benefits
- Breaking of water and methanol azeotropes
- Reduced energy consumption compared to energy-intensive conventional distillation process, like entrainer distillation or pressure swing distillation
- No additional chemicals or entrainers
- Low space requirement (installation in production buildings possible)
- Debottlenecking of existing distillation / dehydration solvent processes
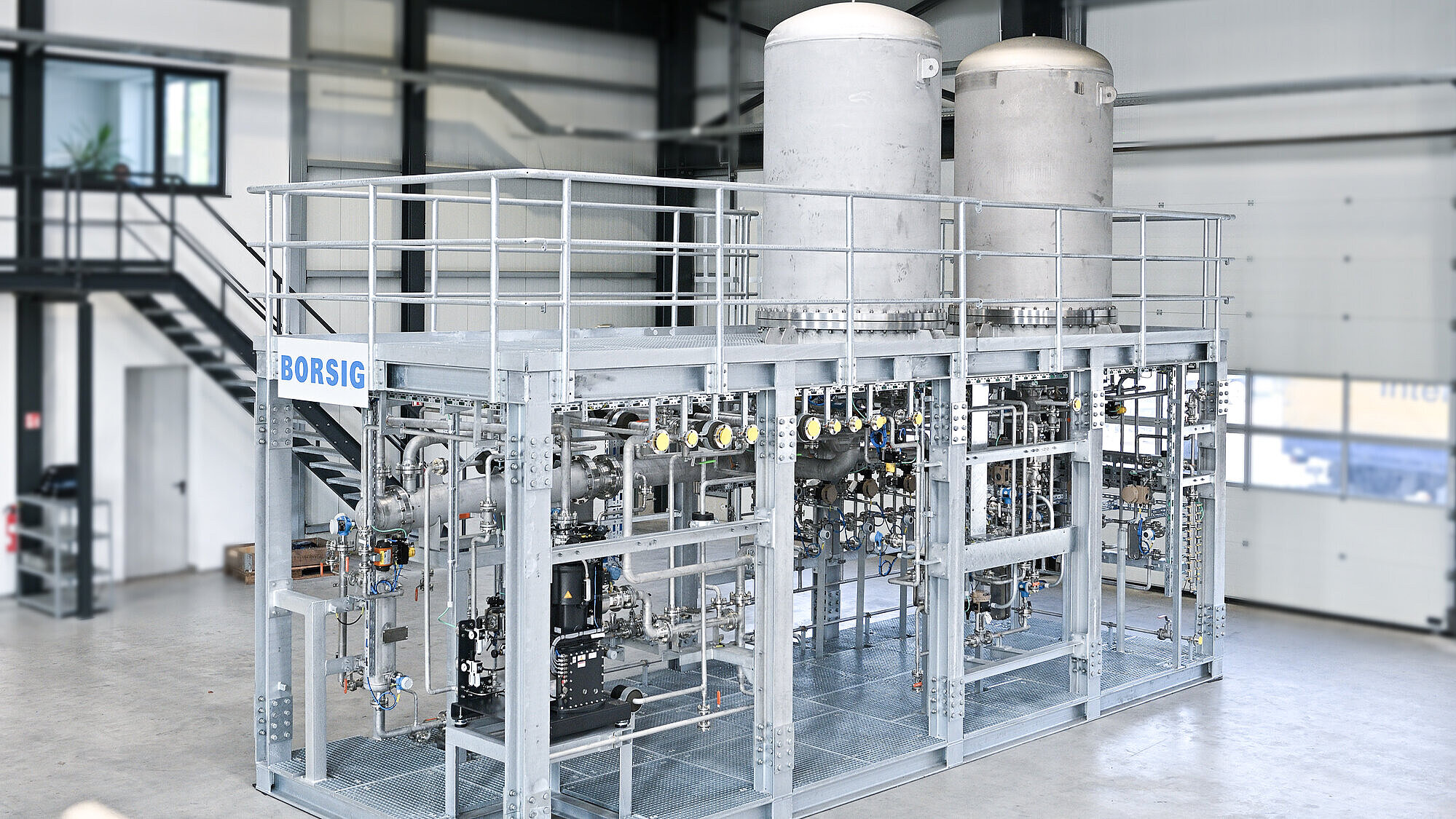
Process
In BORSIG Pervaporation Units , the liquid feed is pre-heated and fed to the membrane modules. Water or methanol is adsorbed on the hydrophilic layer of the membrane and permeates through the membrane. The driving force is the difference in partial pressure between the upper and lower side of the membrane that is kept under vacuum.
The vacuum causes the evaporation and consequently desorption of the permeated component on the lower side of the membrane, the so called “Permeate”. The purified solvent remains on the upper side of the membrane and is routed back to the customer as “Retentate”.