Synthesis gas cooler downstream of partial oxidation of oil and natural gas
The non-catalytic cracking of hydrocarbons by partial oxidation of natural gas, oil etc. is carried out at temperatures up to 1,500 °C and pressures up to 8,000 kPa.
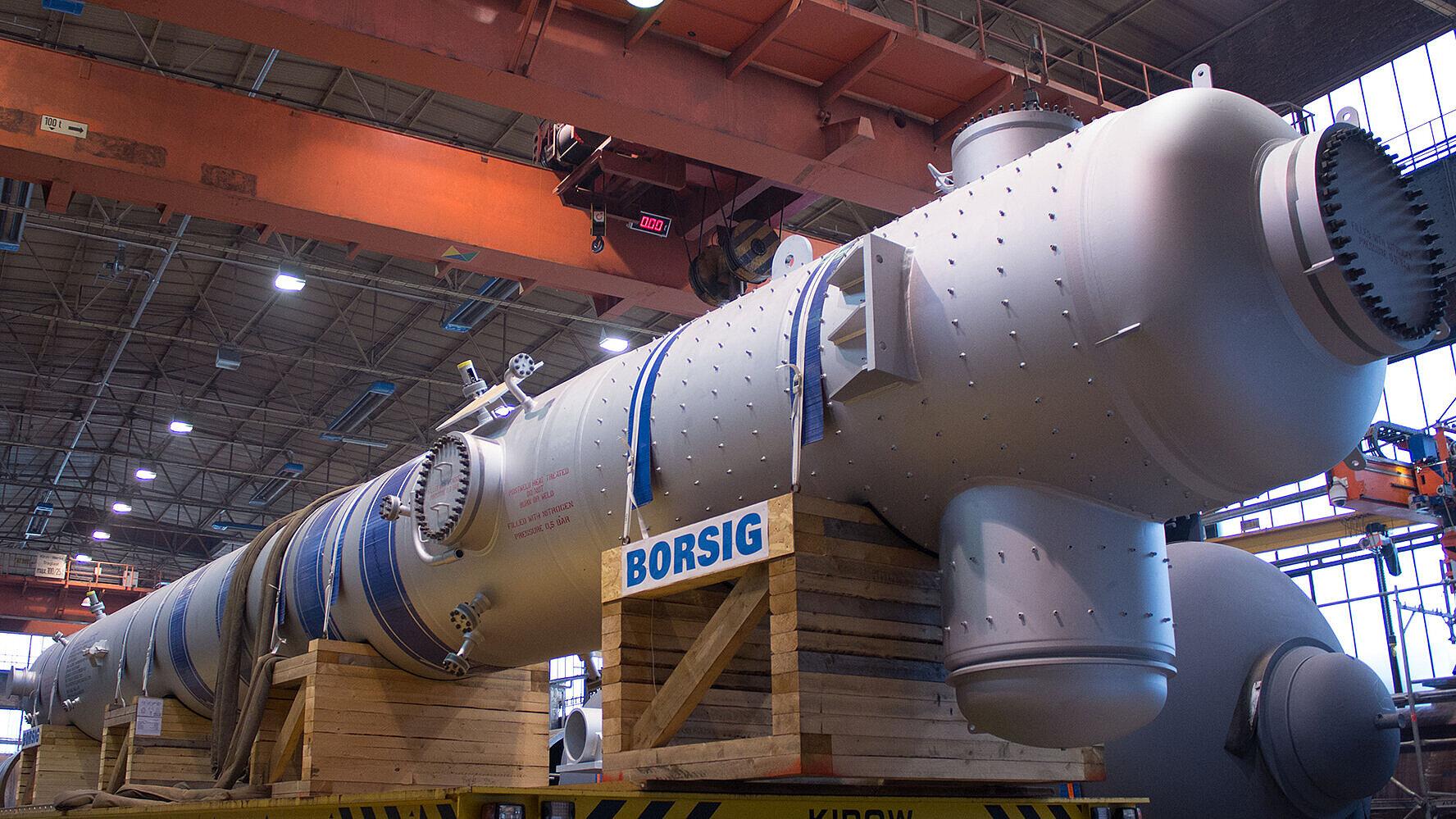
Besides the resulting reaction components CO, CO2, H2, H2O and H2S the process gas is loaded with soot and ash. Depending on the type of feedstock other impurities like vanadium, nickel and iron can also be expected. Due to these impurities, the high particulate burden of the gas and the hydrogen sulfide the waste heat boiler must be highly resistant to erosion, corrosion and fouling.
The process gas has an inlet temperature around 1,500 °C and an outlet temperature of about 300 °C. The heat of the gas is used to generate steam of a pressure of up to 140 bar (14,000 kPa). The heat can also be used to superheat the steam by a superheater integrated into the waste heat boiler.
Until today waste heat boilers were built with a gas side flow rate of up to 70,000 Nm³/h. The design used allows this to be easily expanded to a quantity of 200,000 Nm³/h.
BORSIG Process Heat Exchanger GmbH has developed its own boiler design taking into account the high demands as already mentioned. This boiler design is suitable for all gasification processes.
The waste heat boiler is designed as a fire-tube boiler. The hot synthesis gas enters the heating surfaces with a temperature of about 1,400 °C and is cooled down in these tubes to approximately 300 °C. The heat from the synthesis gas is used for generating saturated steam.The tubes are designed as helically wound heating surfaces. Their diameter usually decreases in four to five steps to keep the gas velocity almost constant while the gas is cooled down. This ensures a self-cleaning effect, which is required when the content of solid particles in the gas is high. A conical inlet section is used to reduce the turbulence at the inlets.
The maximum material stresses occur at the gas inlet nozzles. Therefore their design has to be the focal point of attention. The gas inlet nozzles are provided with a forced circulation. Boiler water is taken from the lower boiler area and supplied to the double tubes in the gas inlet zone by recirculating pumps.
The maximum metal temperatures occur at the inlet of the cone and the transition from the cone to the cylindrical tube.
Two features are implemented to the boiler design to reduce the wall temperature in these sections:
Reinforcement ribs
On the water side the gas inlet nozzles are provided with reinforcement ribs. This allows to reduce the wall thickness and thereby the wall temperatures in this area. This design of the gas inlet nozzles with reinforcement ribs as described here is protected by patent.
Ceramic coating
The application of a ceramic protection coating on the gas side of the inlet nozzles considerably improves the resistance to corrosion and erosion. The coating also reduces the wall temperatures due to its low conductivity.
The special design features and advantages can be summarized as follows:
- The gas inlet nozzles are cooled by forced and natural circulation.
- The gas inlet nozzles are designed with reinforcement ribs on the water side and ceramic coating on the gas side.
- The tube diameters are decreasing in several steps to maintain a minimum gas velocity.
- The tube coils are accessible through the upper and lower manhole and individually replaceable.
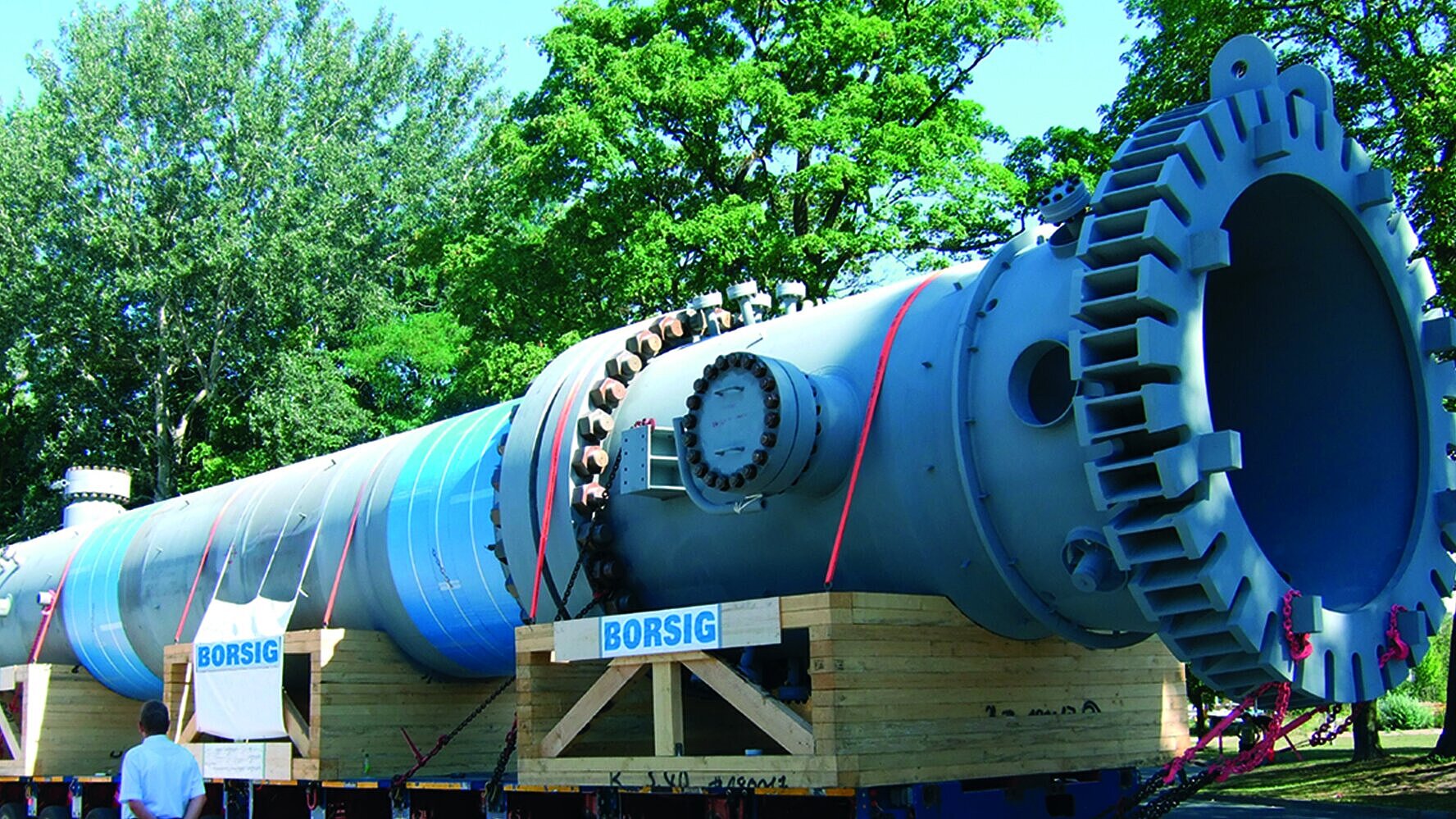
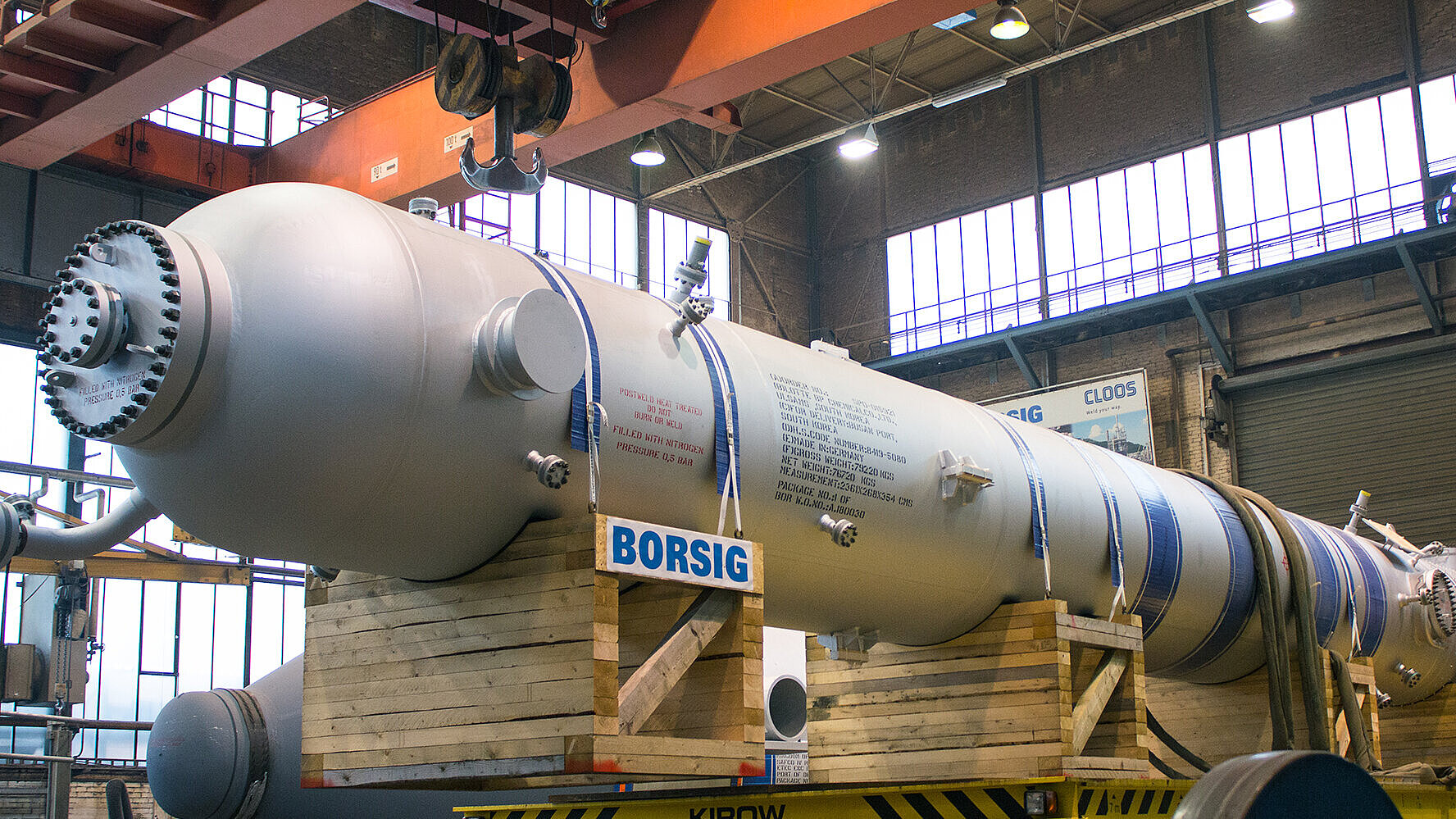