Manufacturing location Berlin - pressure vessels and heat exchangers
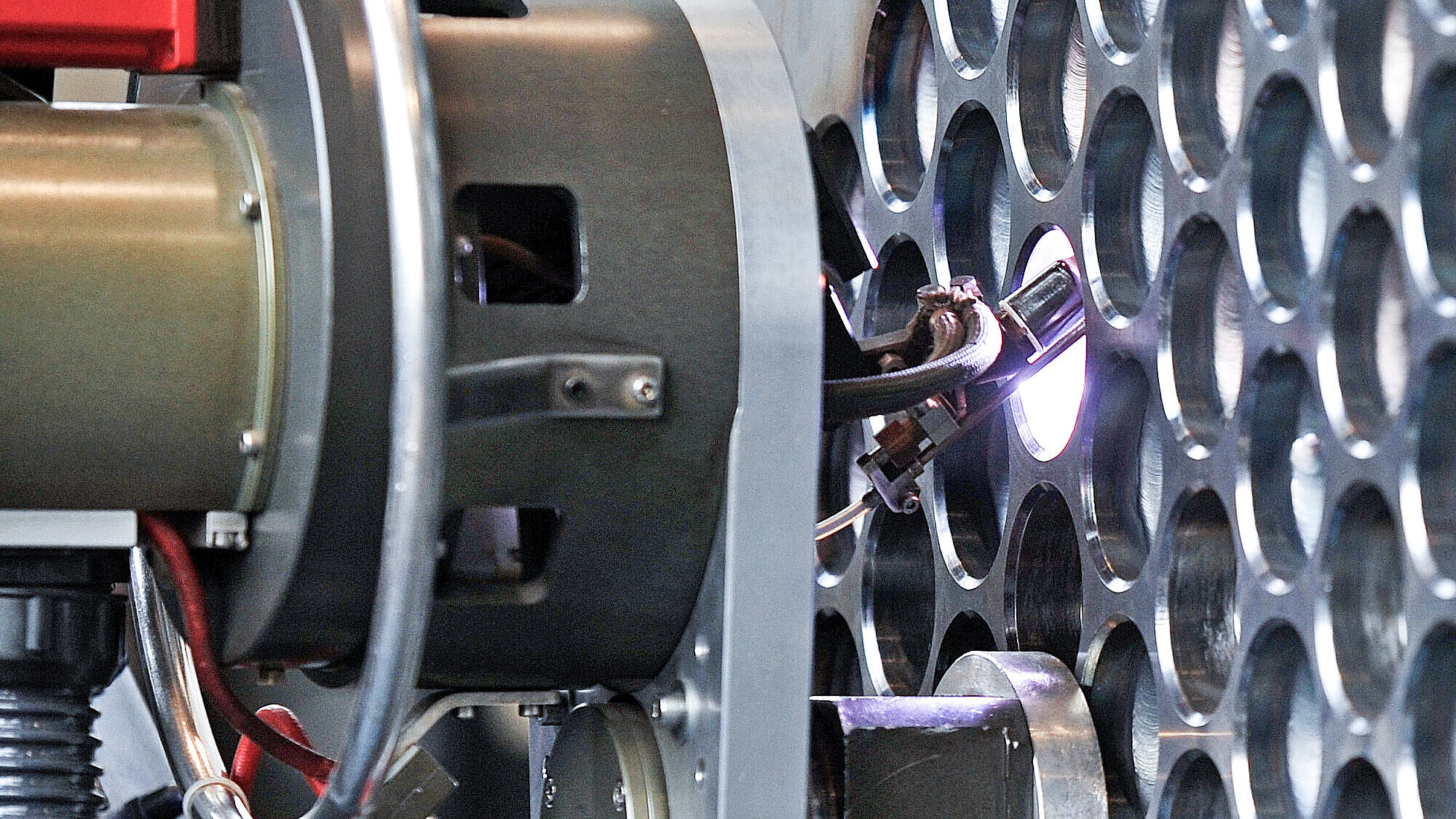
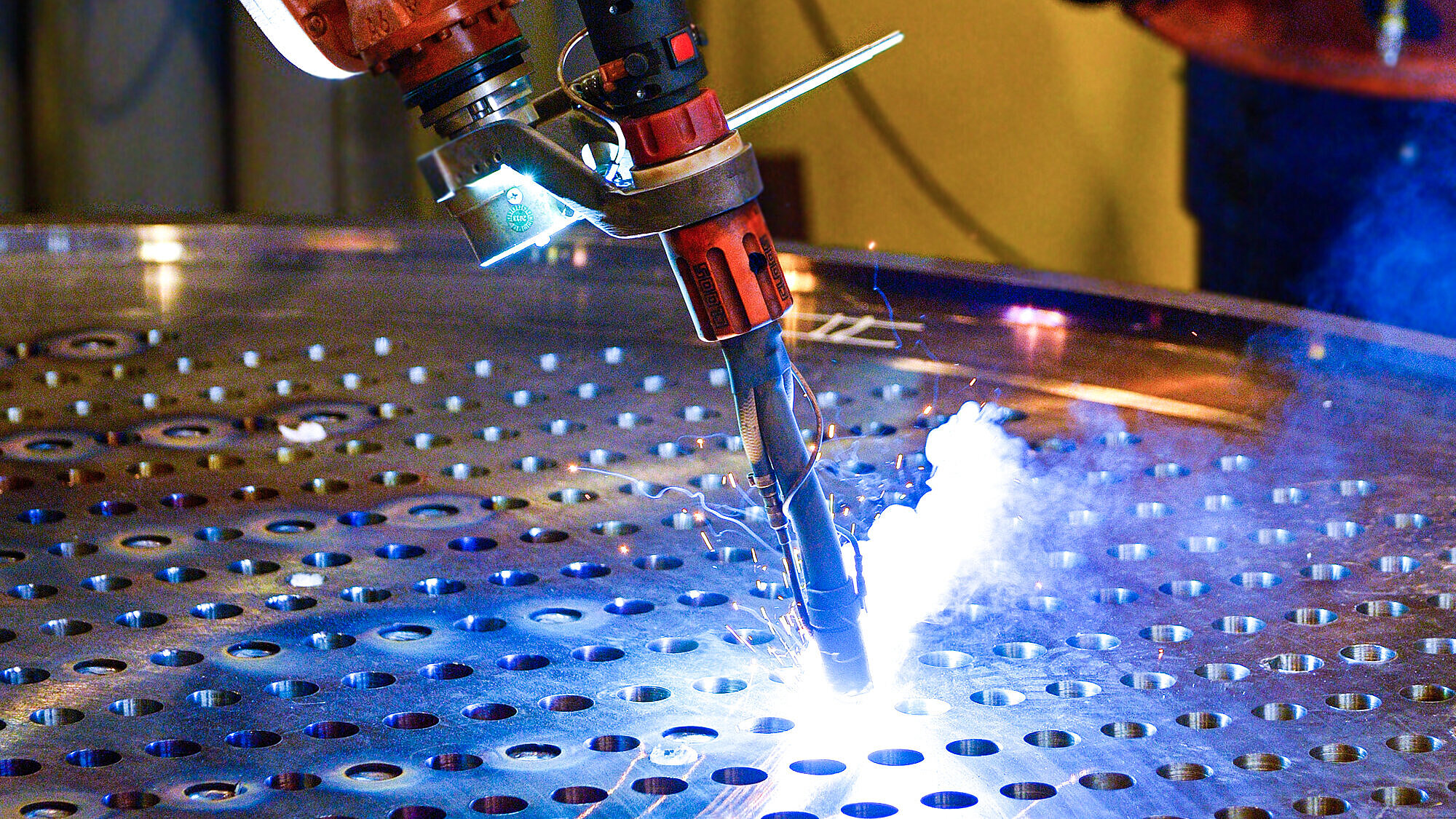
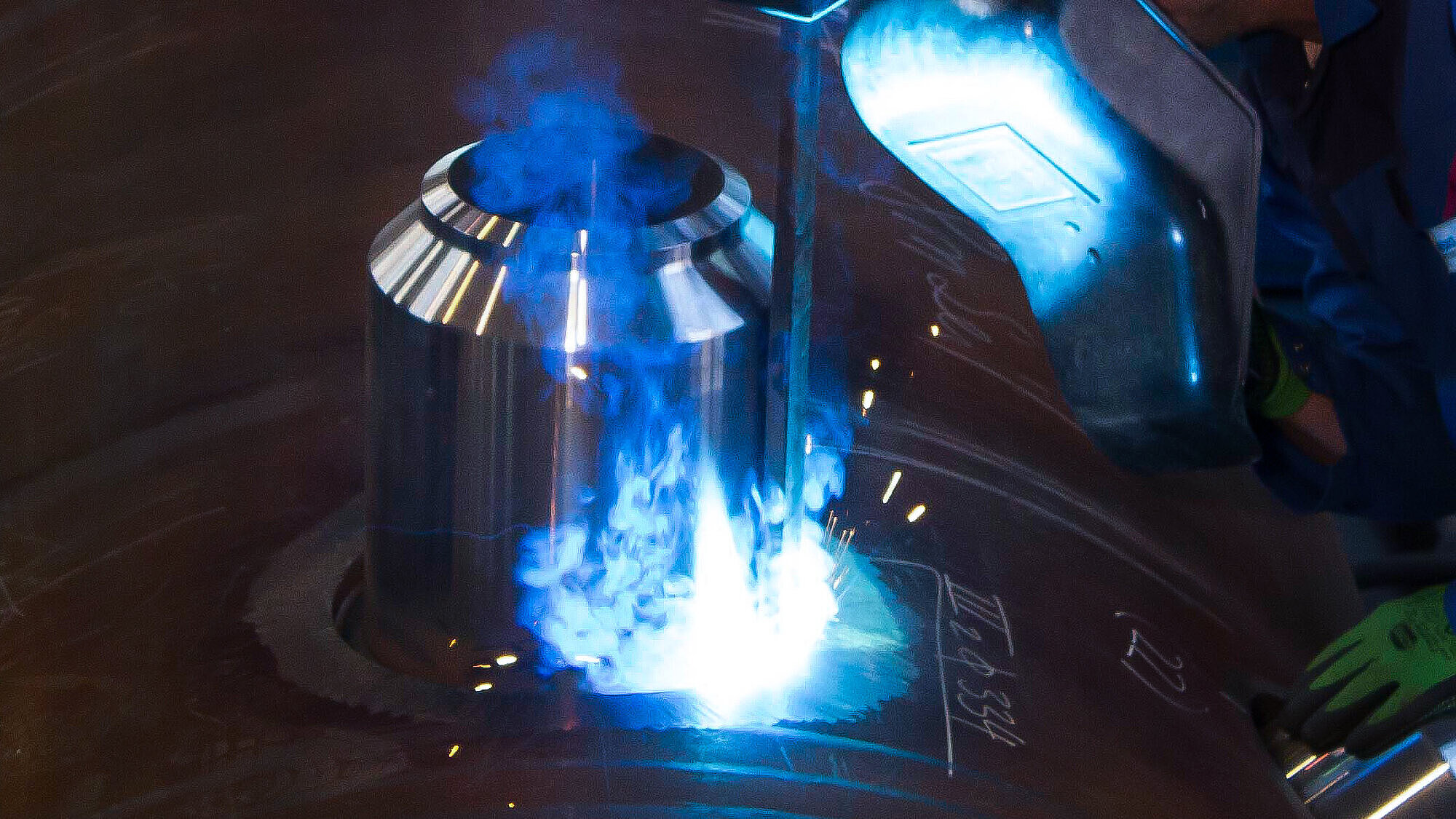
BORSIG Process Heat Exchanger GmbH in Berlin owns more than 16,700 m² of indoor workshop facilities, 6,000 m² open space and is equipped with a 250 t crane capacity.
Our highly qualified staff is fully familiar with all modern production procedures. High-tech welding technology is our core competence. We offer laser controlled welding seam guidance system for submerged narrow-gap welding, the use of robot welding systems for the GMAW welding process in the high pressure vessel manufacture, GMAW narrow gap robot systems with integrated 3D cutter systems plasma and autogenous, TIG hot wire welding, SAW nozzle welding, the automatic tube to tube sheet welding incl. inbore welding of up to 500 mm as well as qualified machining of all steel and nickel-based alloys, electroslag strip cladding and SAW (submerged arc) strip classing.
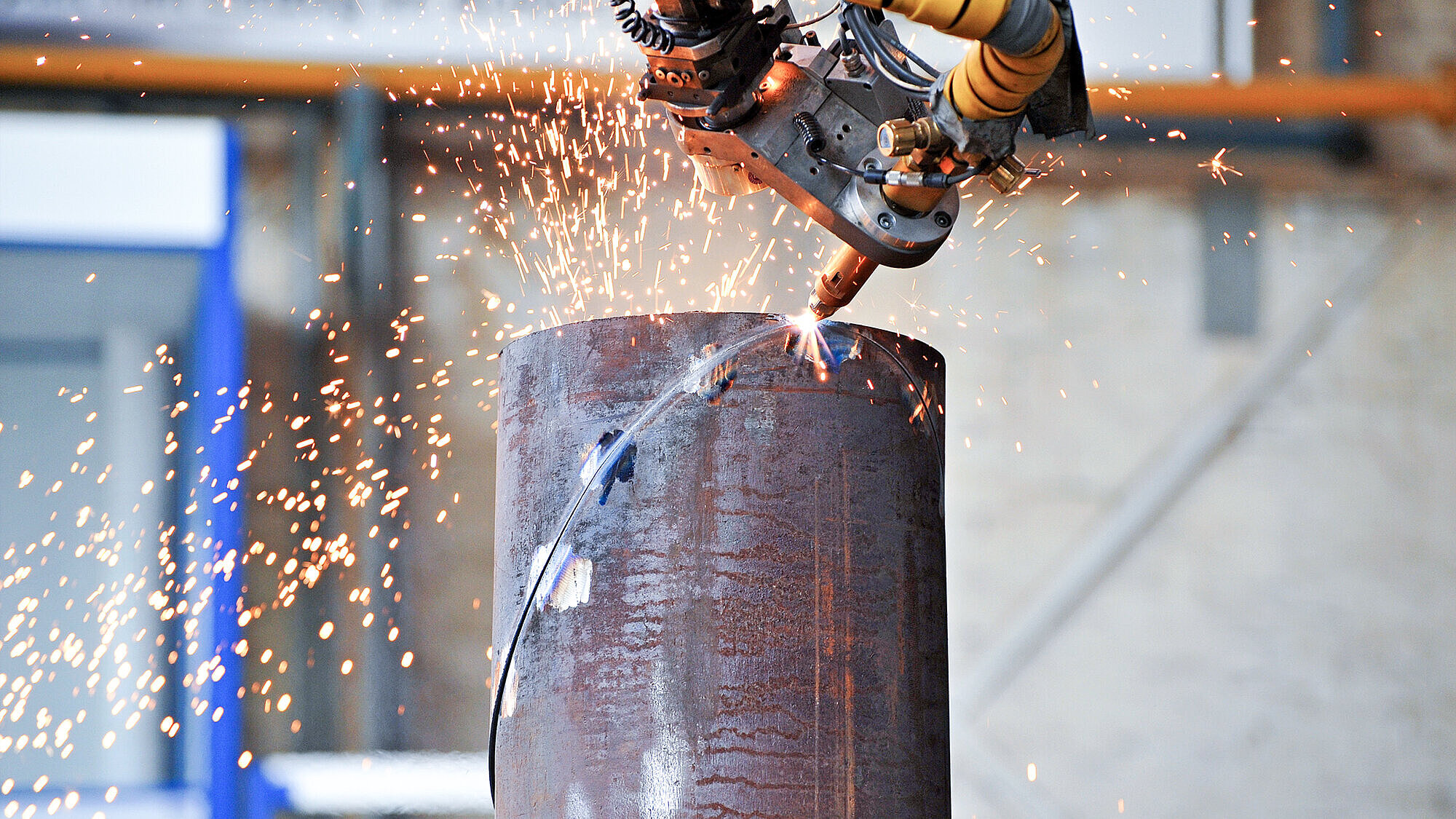
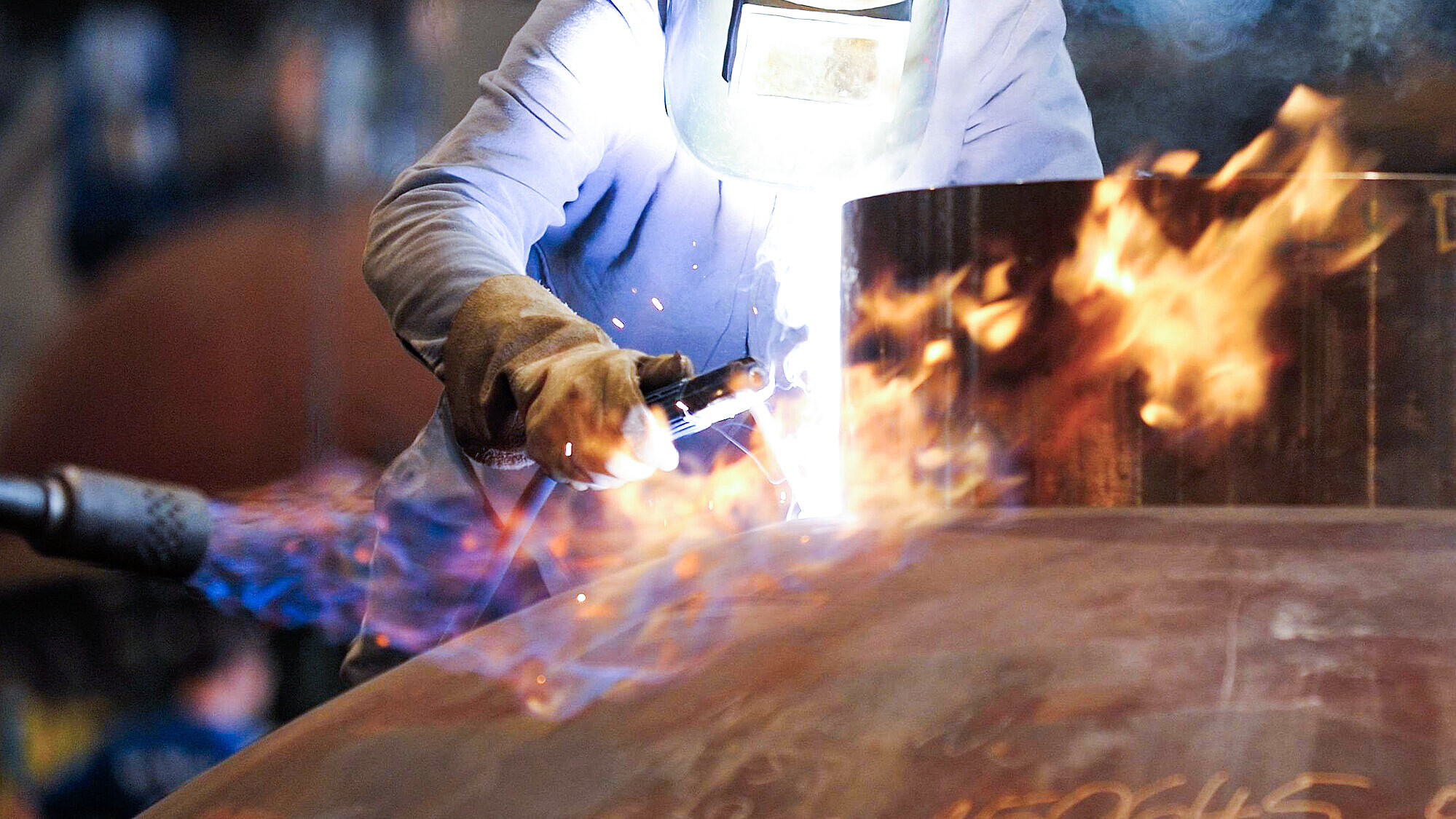
Certificates (extract)
- Quality Management DIN EN ISO 9001
- Environmental Management System DIN EN ISO 14001
- Occupational Safety SCC**
- ASME U, U2, R and S
- SQL licence for PR China
- AD 2000 - Directives HP 0
- TRD 201 and DIN EN ISO 3834-2 and DIN 18800-7
The company has a direct water connection since 2008, the Borsig harbor, so that pressure vessels and heat exchangers of every overall size can be transported easily on the water way.
Machine pool (excerpt)
- robot welding systems
- various semi-automatic welding systems
- nozzle welding machines
- a CNC-controlled cutting machine
- feed-in annealing furnaces equipped for circulating air up to 1,100 °C with fully automatic control systems
- various CNC tool machines
Testing technology
- mechanical-technological tests
- quantomeric analysis
- radiographic tests
- non-destructive testing
- metallography
- damage analysis